
Heterogeneous catalysis and catalyst recycling
Heterogeneous catalysis is a type of catalysis in which the catalyst occupies a different phase from the reactants and products. This may refer to the physical phase — solid, liquid or gas — but also to immiscible fluids. Heterogeneous catalysts can be more easily recycled than homogeneous, but characterization of the catalyst and optimization of properties can be more difficult.


Heterogeneous catalysis is widely used in the synthesis of bulk and fine chemicals. In a general, small scale batch reaction, the catalyst, reactants, and solvent are stirred together until completion of the reaction, after which the bulk liquid is separated by filtration. The catalyst can then be collected for either recycling or disposal. In a continuous process, the catalyst can be fixed in space and the reaction mixture allowed to flow over it. The reaction and separation are thus combined in a single step, and the catalyst remains in the reactor for easy recycling. Beyond facilitating separation, thecatalyst may have improved lifetime due to decreased exposure to the environment, and reaction rates and turnover numbers can be enhanced through the use of high concentrations of a catalyst with continuous recycling. The benefits of flow are seemingly obvious, yet it has only recently become a widely adopted method for bench-scale synthesis.1


The most common application of continuous heterogeneous catalysis is in hydrogenation reactions,2 where the handling and separation of solid precious metal catalysts is not only tedious but hazardous under batch conditions. Moreover, the mixing between the three phases in a hydrogenation is generally quite poor. The use of a flow reactor gives a higher interfacial area between phases and thus more efficient reactions. For example, Ley and co-workers found that the hydrogenation of alkene 1 to 2 was challenging in batch, requiring multiple days at 80 bar of H2 (Scheme 1).3 Using a commercially available H-Cube® reactor, the reaction time was shortened to 4 hours, the pressure reduced to 60 bar, and manual separation and recycling of the catalyst from the reaction was unnecessary. The increased efficiency is due to a combination of improved mixing of the three phases, as well as the continuous recycling and high local concentration of the catalyst. The H-Cube offers a further safety advantage because it generates hydrogen gas on demand from water, obviating the need for a high pressure H2 tank.

![]() | ||
Scheme 1 Hydrogenation with an immobilized heterogeneous catalyst. |
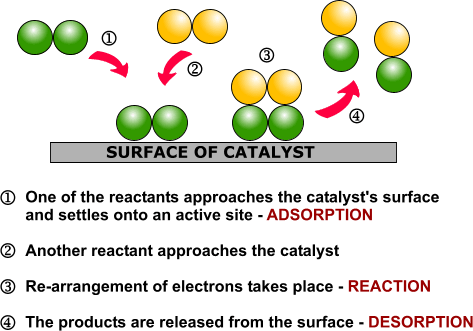
![]() | ||
Scheme 7 Immobilization of a homogeneous catalyst on a solid support. |

![]() | ||
Scheme 3 Automated recycling of a biphasic catalyst system. |
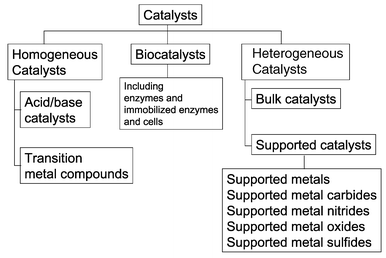
Examples of heterogeneous catalysisThe hydrogenation of a carbon-carbon double bondThe simplest example of this is the reaction between ethene and hydrogen in the presence of a nickel catalyst.![]() ![]() ![]() ![]() ![]() ![]() ![]() Catalytic converters Catalytic converters change poisonous molecules like carbon monoxide and various nitrogen oxides in car exhausts into more harmless molecules like carbon dioxide and nitrogen. They use expensive metals like platinum, palladium and rhodium as the heterogeneous catalyst. The metals are deposited as thin layers onto a ceramic honeycomb. This maximises the surface area and keeps the amount of metal used to a minimum. Taking the reaction between carbon monoxide and nitrogen monoxide as typical: ![]() ![]() | |
Catalytic converters can be affected by catalyst poisoning.
This happens when something which isn't a part of the reaction gets
very strongly adsorbed onto the surface of the catalyst, preventing the
normal reactants from reaching it.Lead is a familiar catalyst poison for
catalytic converters. It coats the honeycomb of expensive metals and
stops it working.In the past, lead compounds were added to petrol
(gasoline) to make it burn more smoothly in the engine. But you can't
use a catalytic converter if you are using leaded fuel. So catalytic
converters have not only helped remove poisonous gases like carbon
monoxide and nitrogen oxides, but have also forced the removal of
poisonous lead compounds from petrol.The use of vanadium(V) oxide in the Contact Process During the Contact Process for manufacturing sulphuric acid, sulphur dioxide has to be converted into sulphur trioxide. This is done by passing sulphur dioxide and oxygen over a solid vanadium(V) oxide catalyst. ![]() ![]() | |
This example is slightly different from the previous ones because the gases actually react with the surface of the catalyst, temporarily changing it. It is a good example of the ability of transition metals and their compounds to act as catalysts because of their ability to change their oxidation state. | |
The
sulphur dioxide is oxidised to sulphur trioxide by the vanadium(V)
oxide. In the process, the vanadium(V) oxide is reduced to vanadium(IV)
oxide.![]() ![]() ![]() ![]() |

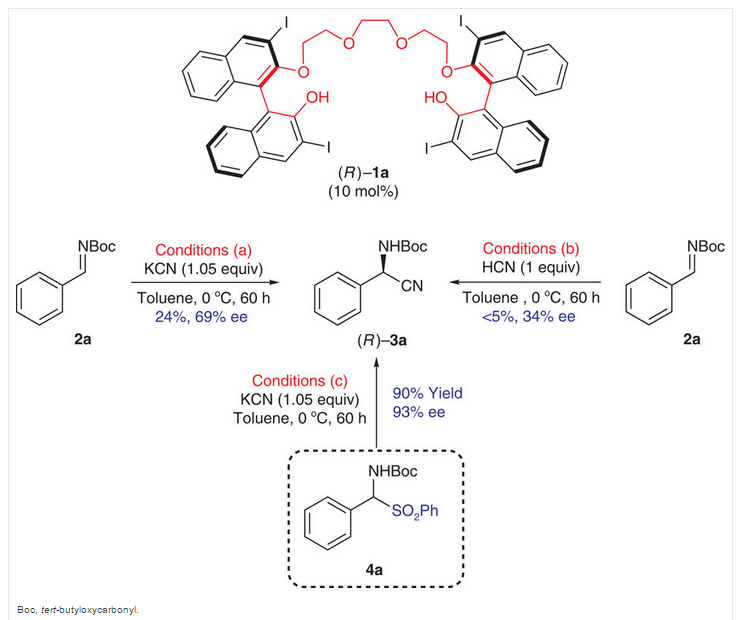

- C. G. Frost and L. Mutton, Green Chem., 2010, 12, 1687–1703 .
- M. Irfan, T. N. Glasnov and C. O. Kappe, ChemSusChem, 2011, 4, 300–316
- C. F. Carter, I. R. Baxendale, M. O'Brien, J. P. V. Pavey and S. V. Ley, Org. Biomol. Chem., 2009, 7, 4594–4597 .
- P. McMorn and G. J. Hutchings, Chem. Soc. Rev., 2004, 33, 108–122.
- S. Ceylan and A. Kirschning, in Recoverable and Recyclable Catalysts, ed. M. Benaglia, John Wiley & Sons Ltd, 2009, pp. 379–410 .
- A. J. Sandee, D. G. I. Petra, J. N. H. Reek, P. C. J. Kamer and P. W. N. M. Van Leeuwen, Chem.–Eur. J., 2001, 7, 1202–1208
- M. Pagliaro, V. Pandarus, R. Ciriminna, F. Belénd and P. D. Cerà, ChemCatChem, 2012, 4, 432–445 .
- C. W. Kohlpaintner, R. W. Fischer and B. Cornils, Appl. Catal., A, 2001, 221, 219–225
- W. A. Herrmann, C. W. Kohlpaintner, H. Bahrmann and W. Konkol, J. Mol. Catal., 1992, 73, 191
- A. B. Theberge, G. Whyte, M. Frenzel, L. M. Fidalgo, R. C. R. Wootton and W. T. S. Huck, Chem. Commun., 2009, 6225–6227 .
- A. Yoshida, X. Hao and J. Nishikido, Green Chem., 2003, 5, 554–557 .
- E. Perperi, Y. Huang, P. Angeli, G. Manos, C. R. Mathison, D. J. Cole-Hamilton, D. J. Adams and E. G. Hope, Dalton Trans., 2004, 2062–2064 .
- S. Liu, T. Fukuyama, M. Sato and I. Ryu, Org. Process Res. Dev., 2004, 8, 477–481
- T. Fukuyama, M. T. Rahman, M. Sato and I. Ryu, Synlett, 2008, 151–163
- J. F. B. Hall, X. Han, M. Poliakoff, R. A. Bourne and M. W. George, Chem. Commun., 2012, 48, 3073–3075 .
- R. A. Bourne, X. Han, M. Poliakoff and M. W. George, Angew. Chem., Int. Ed., 2009, 48, 5322




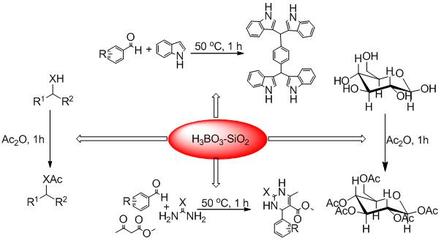

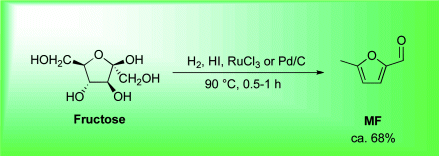



//////